ООО «Гипрохлор» (ранее ОАО «Востсибхимпроект») являлся генпроектировщиком по данному проекту.
В 2002 году было разработано «Обоснование инвестиций», после его утверждения на Совете директоров ОАО «Саянскхимпласт», был выполнен ТЭО (проект), который в августе 2003 года прошел Государственную экспертизу. Иностранным партнером по проекту Конверсии выступала немецкая инжиниринговая фирма «Хемианлагенбау Хемниц ГмбХ» (САС), бывший филиал «Лурги Лайф Сайенс» в Хемнице. Фирма САС разрабатывала проект, поставляла оборудование, осуществляла шеф-монтаж и пуско-наладку стадий, электролиза, обработки анолита и католита, охлаждения водорода, обработки деминерализованной воды. Также в составе поставок фирмы САС были предусмотрены комплектные установки: ионообменной очистки рассола (фирма KB-tec, Германия), синтеза соляной кислоты (фирма SGL Carbon Германия), выпаривания серной кислоты (фирма QVF, Германия), выпаривание натрового щелока (фирма Bertrams, Швецария). Инжиниринг, шеф-монтаж и пуско-наладку по данным установкам, осуществлялся специалистами данных фирм. Поставщиком основного оборудования, мембранных электролизеров, являлась Японская фирма «Асахи Касей», мировой лидер по мембранной технологии производства хлора и соды каустической.
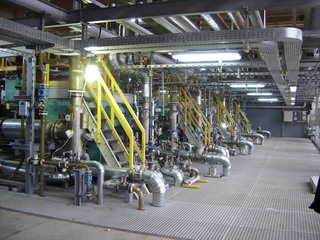
Необходимо особо отметить фирму «Синетик» Новосибирск, которая на подряде у ООО «Гипрохлор» осуществляла комплексный проект автоматизации всего мембранного производства, так называемый верхний уровень АСУТП.
ООО «Гипрохлор», как генпроектировщику, приходилось решать непростые задачи, а именно, как при работающем ртутном производстве, обеспечить подготовку всех стадий мембранного производства, а затем в течение двух месяцев осуществить перевод остановленного ртутного производства на мембранную технологию. Кроме того, ООО «Гипрохлор» осуществлял проектирование основных технологических стадий, которые не входили в объем работ иностранных фирм, это:
- Рассолопромысел. Впервые в России необходимо было обеспечить использование в качестве растворителя обедненный анолит мембранного производства, т.е. обеспечить его донасыщение в скважинах. Применяя различные «ноу-хау», было спроектировано новое КРП (контрольно-распредилительный пункт), хозяйство нерастворителя, емкостной парк, система АСУТП рассолопромысла.
- Стадия содово-каустической очистки рассола. В качестве основных аппаратов, были разработаны и применены осветлители рассола КС 300, которые при небольших габаритных размерах обеспечивали высокую производительность очистки рассола и хорошо управлялись от системы АСУТП. Соответственно были спроектированы узлы приготовления и подачи реагентов, сбора и вывода шлама, и.т.д.
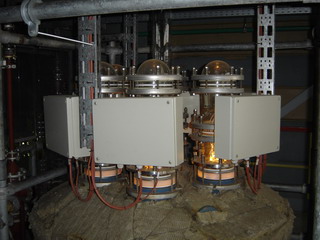
- Стадия механической фильтрации рассола. Действующие титановые фильтра ЛВАЖ-250Т, были переведены на схему с фильтровспомагательным слоем, в качестве которого была применена альфа целлюлоза. Кроме того фильтра были адаптированы в систему АСУТП.
- Стадия сбора и нейтрализации сточных вод. Концепцией проекта обеспечивалось максимальное использование сточных вод с возвратом их в производство. Был разработан и спроектирован узел приема и обработки сточных вод. Сточные воды доводились до регламентного значения и отправлялись с анолитом на донасыщение в скважины рассолопромысла.
- Узел подачи водорода потребителям. Учитывая работу мембранных электролизеров под давлением, специалистами ООО «Гипрохлор» была предложена схема подачи водорода на синтез соляной кислоты и на производство пара без компрессоров. При проектировании данного узла были применены нестандартные решения.
- Отделение охлаждения, сушки и компримирования хлора. Основная задача состояла в обеспечении надежности работы данных стадий и адаптация их в систему АСУТП. Впервые в России хлорные компрессора были переведены на автоматическое управление, использование принципа работы электролизеров под давлением в хлорном пространстве, позволило повысить эффективность системы сушки хлора и обеспечить стабильность работы хлорных компрессоров.
- Вакуумное и химическое обесхлоривание анолита. Отделение подверглось существенной реконструкции, как технологической, так и изменением системы управления (внедрение АСУТП).
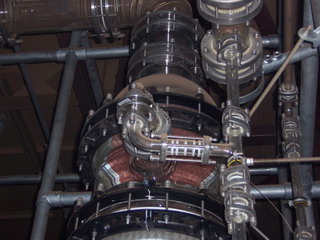
- Выпрямительные агрегаты. Для обеспечения ртутного производства постоянным током, ООО «Гипрохлор» был выполнен проект шинного моста, который в дальнейшем использовался для подключения мембранных электролизеров. Для соединения пакета алюминиевых шин, было применено новое решение, исключающее потерю напряжение в сварных стыках. Самая трудная и важная задача состояла в обеспечении регулирования величины постоянного тока от АСУТП. Фирмой «Синетик» был разработан специальный блок, с помощью которого удалось решить данную задачу.
- Система аварийного поглощения хлора. Проектом изменена система ввода хлорсодержащих абгазов, на хлорной системе в отделении сушки хлора установлен дополнительный гидрозатвор, применены новые вентиляторы, позволяющие поддержиавать необходимое разряжение в системе. Вся установка адаптирована в АСУТП.
- Межцеховые коммуникации (МЦК). Были максимально использованы действующие эстакады а также предусмотрены новые. Применены не используемые трубопроводы. Изменена система подачи оборотной воды в цех электролиза.
- Демеркуризация ртутного загрязнения. На подряде у ООО «Гипрохлор» данную работу выполнил СП «Еврохим» г. Киев. Специалисты данного предприятия имеют большой опыт выполнения проектов подобного рода, и являются единственными в СНГ, занимающимися ликвидацией ртутных загрязнений подобного рода. В целом проект демеркуризации состоял из трех этапов, это демеркуризация корпусов в которых размещались установки мембранного электролиза, затем при останове ртутного производства, демонтаж зартученного оборудования с демеркуризацией строительных конструкций, и заключительный этап, это экранирование площадей, а также полигона захоронения ртутьсодержащих отходов. Создание сети мониторинга.
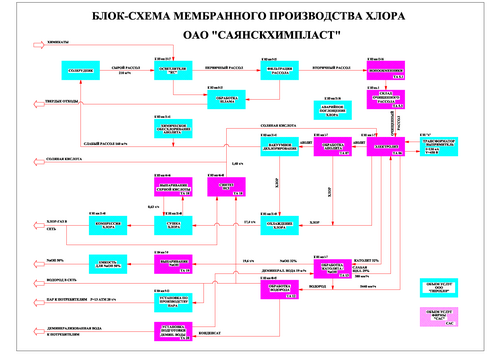